Factories
We’re committed to making clothes with a smaller environmental impact in places that treat workers well. So, when it comes to choosing where we make our clothes, we look at a number of different factors - quality, price, speed, reduced environmental impact, and working conditions for the people in the facility. Our partners share a common vision of sustainability, accountability, and transparency. We published Our Factories list so you can learn more about the factories behind our clothes. Transparency is key to accountability, which is why we disclose 100% of Tier 1 finished goods manufacturers and subcontractors within our supply chain. We have aligned with the Transparency Pledge and are participating in the Open Apparel Registry (OAR) to expand on the details that are made public so we can be more accountable for the working conditions in our partner factories.
We currently require all our direct cut, sew & finish manufacturing partners to adhere to our Code of Conduct and additional policies (basically our requirements for ethical operations), and be monitored for compliance and continuous improvement. Our Code of Conduct references the FLA Workplace Code of Conduct which is based on International Labor Organization (ILO) standards and internationally accepted good labor practices.
We require our Tier 1 suppliers to participate in independent, third-party social assessments to ensure fair, safe and healthy working conditions throughout our supply chain. Our assessments are conducted not only to help evaluate our supplier’s overall compliance but to also identify progress and stimulate improvement. All substandard audit findings must be remediated in a timely manner.
Our sustainable partners process:
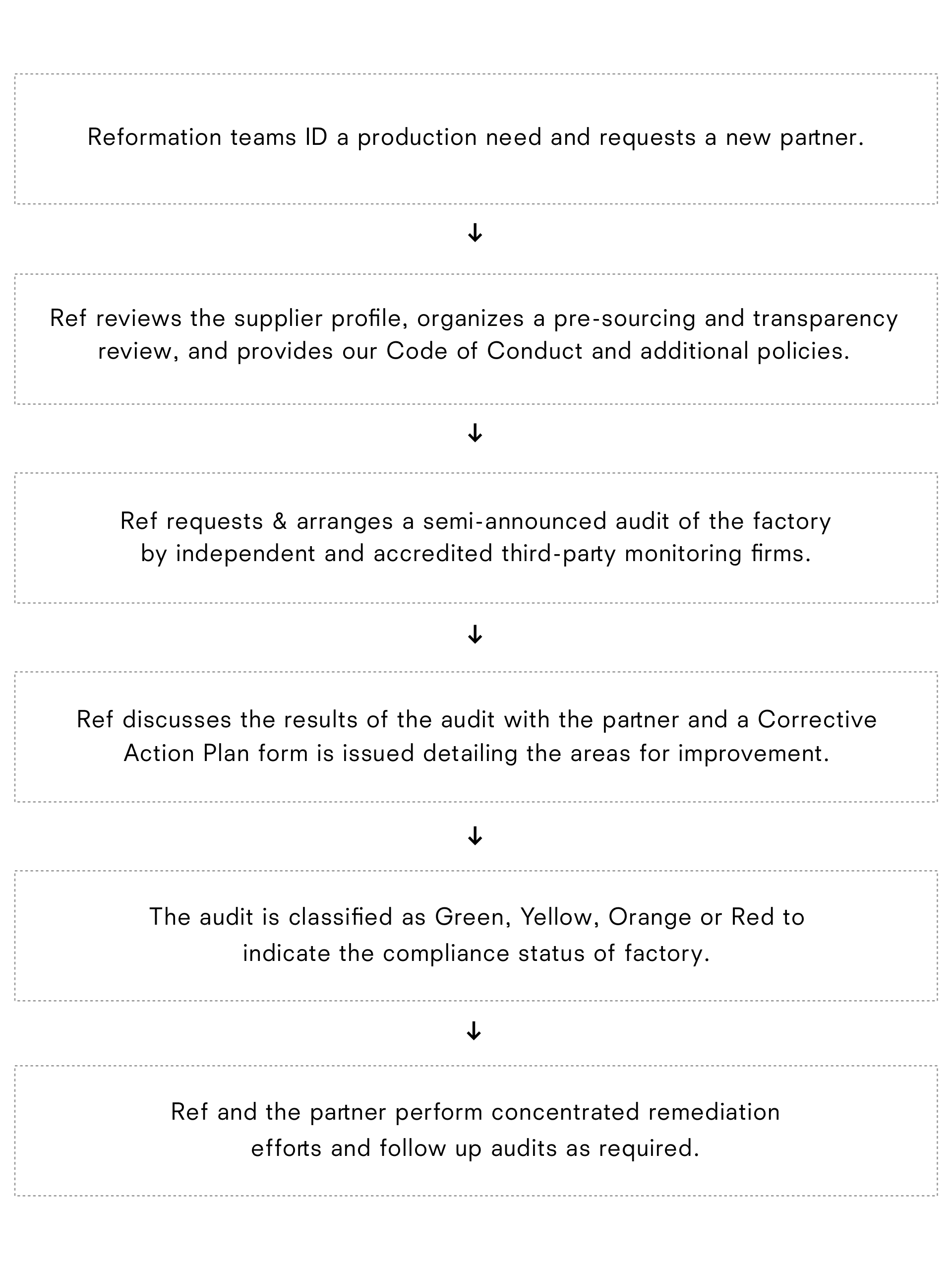
Reformation teams ID a production need and requests a new partner.
↓
Ref reviews the supplier profile, organizes a pre-sourcing and transparency review, and provides our Code of Conduct and additional policies.
↓
Ref requests & arranges a semi-announced audit of the factory by independent and accredited third-party monitoring firms.
↓
Ref discusses the results of the audit with the partner and a Corrective Action Plan form is issued detailing the areas for improvement.
↓
The audit is classified as Green, Yellow, Orange or Red to indicate the compliance status of factory.
↓
Ref and the partner perform concentrated remediation efforts and follow up audits as required.
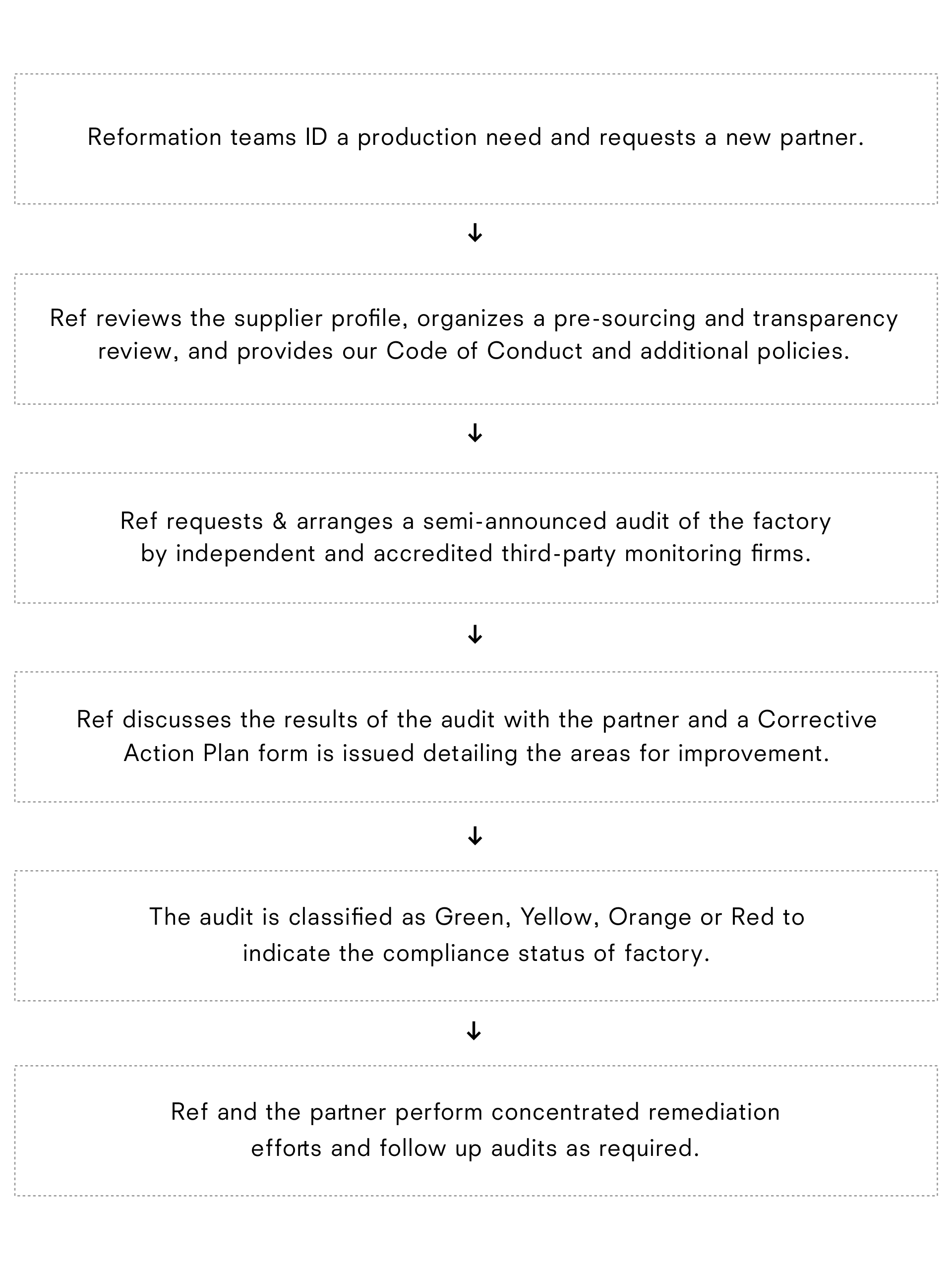
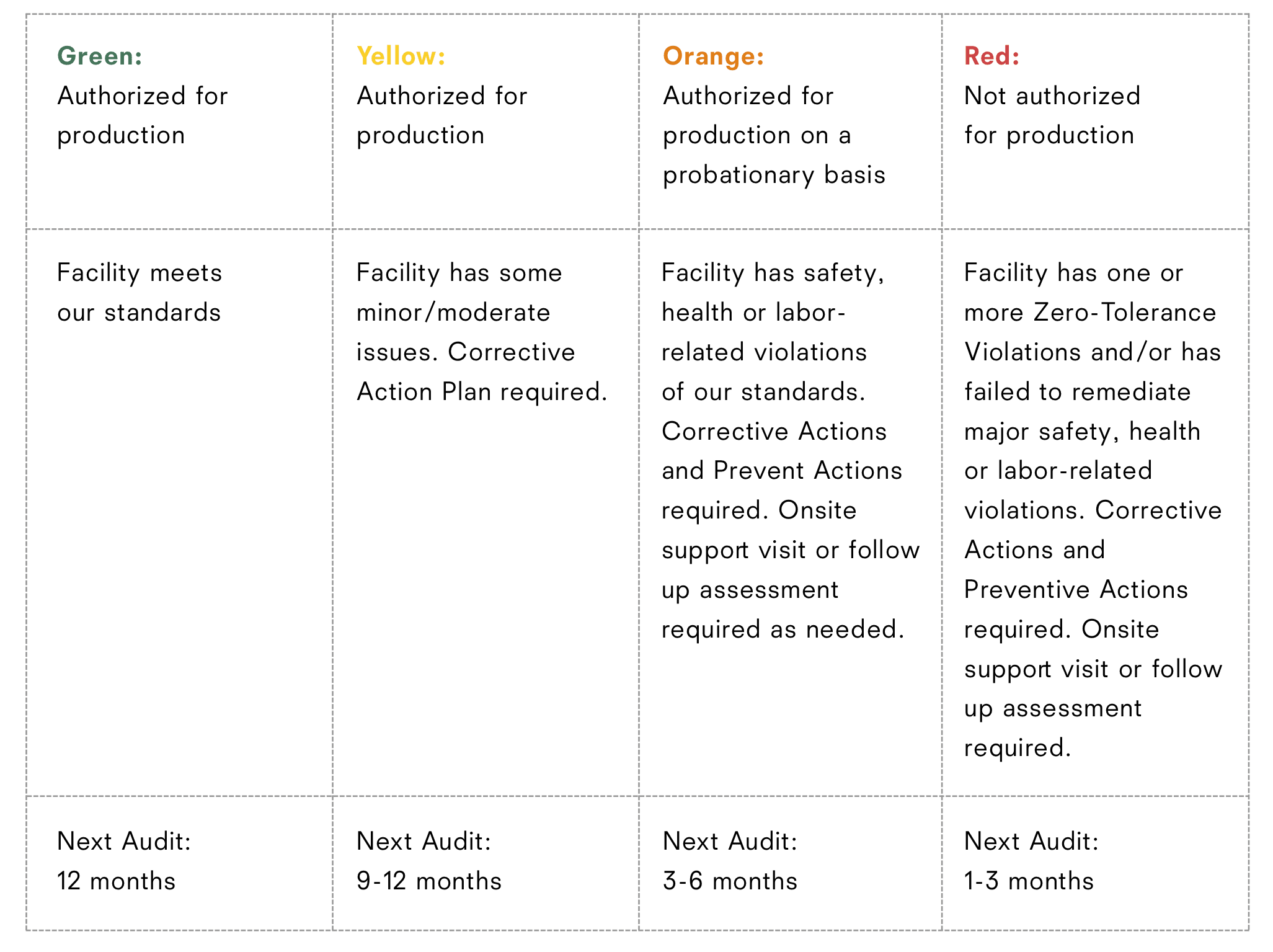
Ratings of all of our vendors*
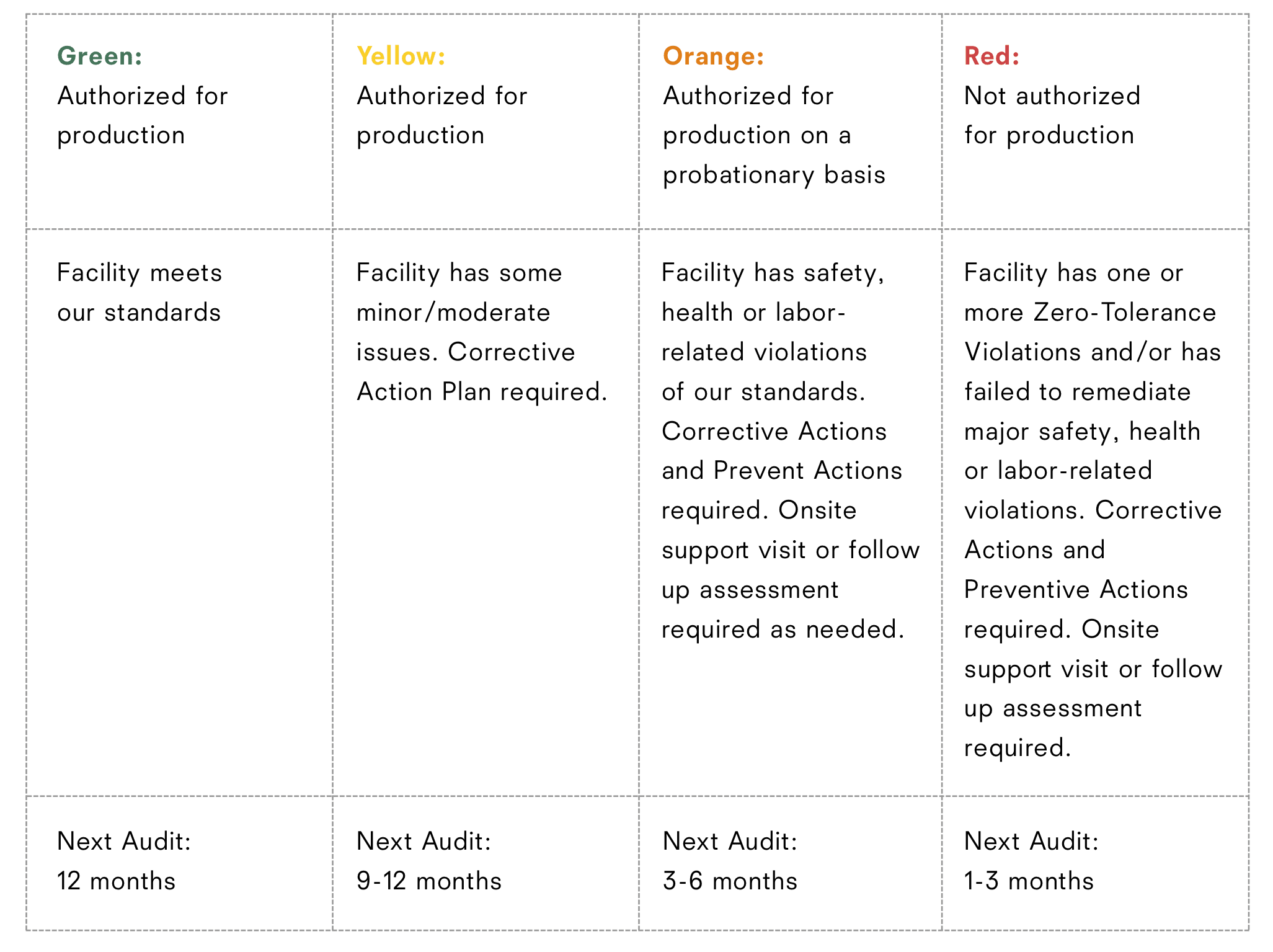
Ratings of all of our vendors*
In order to better understand our purchasing practices, we have been participating in surveys through the Better Buying initiative since 2019. This allows us to receive anonymous feedback and data-driven insights into our purchasing activities and provides recommendations on improvements. Our recent feedback shows that we need to focus on improving the area of Planning and Forecasting. We’re evaluating how we can improve in this area to ensure that we are setting our suppliers up for success in upholding our contractual terms and our standards around safe, healthy and fair working conditions.
COVID-19 Update
The COVD-19 pandemic has posed economic challenges and far-reaching effects to businesses. In line with our commitment to collaborative supplier relationships and worker well-being in our supply chain, we are working closely with our suppliers to find the best way through the global COVID-19 pandemic.
We took full responsibility – and paid in full – for all complete and in-progress finished goods orders. While we extended our payment terms temporarily for a limited amount of agents and in limited cases, we are back to our original terms with all supply chain partners. Our current terms are consistent with industry practice, and we have not asked for any discounts on payments.
Our teams are staying in close conversation with suppliers and we are factoring their circumstances into our decisions to ensure we are doing our part to protect global garment workers in our supply chains.
Currently, the survey is limited to our international vendors in China, Turkey, Mexico and India, with the goal of extending it to our domestic vendors in 2021. The survey covers questions related to happiness at work, relationships with supervisors, trust in grievance mechanisms, working hours, and wages. Some of the most common findings we have seen are: workers do not feel comfortable talking to their direct supervisor if they have a suggestion or complaint; workers do not think their feedback will be treated seriously by the management team; workers do not understand how their wages are calculated.
We address the results from these surveys through our Corrective Action Plan (CAP) management system, where we provide recommendations for each issue noted within the Survey Report. This process allows us to track the progress of corrective and preventative actions with facility management to ensure worker concerns are being addressed proactively.